The SKF Connected Ecosystem:
Empowering Equipment Uptime
3: Inform
1: Connect
2: Detect
4: Improve
Connect
Detect
Inform
Improve
Click on each globe below to find out more
Contact Us
Compare SKF Technologies
Select the right connected technologies and condition monitoring solutions based on your asset criticality and failure mode detection horizon.
Balance-of-plant – offline portable systems: Failure in months to years. Many kinds of assets. Periodic measurements. Weekly or monthly data.
Production semi-critical assets – online wireless system:
Failure in days to weeks. Constant loads and speeds. Periodic measurements. Daily or weekly data.
Production critical assets – online wired system:
Failure in hours to days. Variable loads and speeds. Continuous measurements. Seconds to minutes data.
Data Acquisition
Connectivity
Fault Detection
Data Acquisition Frequency
Speed Restrictions
Variable Condition Load, Speed, etc.
Vibration & Temperature
Process Data Load, Speed, etc.
Live Alarm Monitoring
Man away from Machine
Dashboard Access
Offline
Manual
Wireless + Handheld
Months
Monthly or quaterly
120 RPM onwards
Manual input
Online
Automated
Wireless
Days
Daily monitoring
600 RPM onwards
Online Automated
WireD
Hours
24x7 CONTINUOUS MONITORING
NO RESTRICTIONS
aUTOMATED ANALOGUE & dIGITAL
FULL CAPABILITY
Interpret 'big data' to identify anomalies and diagnose faults with a combination of cloud based IoT solutions and AI driven analytics, expertly validated by our application engineering experts.
Remote Diagnostic Centre:
Data Management:
Failure Modes Detection:
Alarm Management System:
Database parameters are set to detect machine condition that will eventually lead to failure.
Identify defects such as looseness, alignment, unbalance, bearing faults, gear wear, coupling issues, lubrication problems etc. for proactive maintenance actions.
Ability to integrate operation and condition data, resulting in performance monitoring and improvement.
Sophisticated Alarm Management Systems acting as first line of defense and for early detection of anomalies.
Capturing transient events that can affect the life and condition of the machine.
Proactive approach, preventing unplanned downtime.
High resolution spectral data, customized as per application being monitored.
Secure Cloud based environment delivering 24/7 access to machine data, that helps in condition-based decision making.
Interpreting critical machine data to improve machine efficiency.
Monitor equipment in real time, detecting anomalies using a range of sensors and analytical tools.
Provide early warning notifications when potential issues are detected.
Based on data analysis and interpretation, provide recommendations for predictive maintenance.
Translate the anomalies detected into actionable insights advising your operations and maintenance when a problem arises, and how to resolve it with proactive measures.
Dashboard
Easy to interpret, real time dashboard for monitoring machine condition.
Ability to customize visuals and integrate with BI tools.
Hierarchical setup that can be drilled in from site to plant to asset level depiction.
Condition Monitoring Reports, hosted on a web-based platform that is 24/7 accessible from any location.
Providing your operations and maintenance teams with corrective actions and recommendations to keep your key rotating assets running at the performance you need.
Machine condition codes based on severity and consequence, helping in prioritizing actions.
Reports:
Modbus TCP/IP and Modbus RTU capabilities including multiple and simultaneous use.
API and OPC capabilities for Software data communication.
Data is always accessible to make timely changes that can help avoid unplanned downtime.
Integration with Site Systems:
Insights:
Generate machinery insights to help make more informed decisions to improve machine health.
Identify areas of improvement that can add maximum value in improving rotating equipment performance.
Optimize spares and inventory with planned maintenance actions.
SKF's technology and domain expertise increases Smelter Fan mean time between failures
Harness SKF application engineering knowledge to improve reliability based on data-driven decisions by implementing changes to maintenance schedules, upgrades to equipment components,
or improvements to operating procedures.
Spares optimization with SKF's advanced monitoring system
Save time and money with SKF Remanufacturing
SKF Connected Ecosystem
Click on the arrows above to find out more
Click on the icons below to read the case studies.
SKF Technology Comparison
NO CAPABILITY
PARTIAL CAPABILITY
SKF Connected Technologies provide real-time monitoring and predictive analytics by using a variety of sensors to collect data and implement advanced analytics to predict failures.
SKF's process of Connect, Detect, Inform, and Improve makes the path to the center of optimizing performance while minimizing waste and emissions.
Click the SKF Connected Ecosystem Globe to find out more.
Compare SKF Technologies
1
2
3
4
1
2
3
4
Click on the arrows above to find out more
1
2
3
4
Click on the arrows above to find out more
1
2
3
4
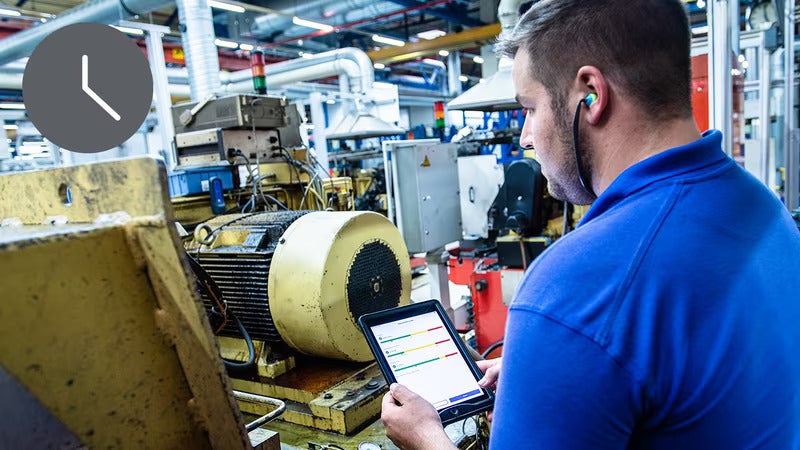